How to Remove Burn Marks from Wood [In 9 Simple Ways]
Burn marks are one of the biggest problems on wood or furniture as they can only be repaired with greater effort. With the right methods and detailed instructions, you can learn how to remove burn marks from wood.
Steps to do it:
- Mix equal parts toothpaste and baking soda in a small bowl to form a thick paste. Start with 1 tsp of each and adjust consistency as needed.
- Apply the paste directly onto the burn-marked wood area using your finger or a soft cloth, following the direction of the wood grain. Be gentle to avoid damaging the wood surface.
- Allow the paste to sit on the burn mark for 5-10 minutes to work its bleaching action.
- Wipe away the paste with a clean, dry cloth. You may need to lightly rub the area to remove any residue.
- For stubborn wood burns, reapply the paste and let it sit a bit longer before wiping it clean.
- Buff the treated area with a soft cloth to restore the wood’s original shine.
Method to Remove Burn Marks from Wood | Wood Types | Furniture Types | Burn Severity |
---|---|---|---|
Mayonnaise | Softwoods like pine | Tables, chairs, cabinets | Light surface burns |
Toothpaste + Baking Soda | All wood types | Tables, chairs, shelves, frames | Light to medium burns |
Cigarette Ash + Lemon Juice | Hardwoods like oak, maple | Tables, desks, shelves | Light surface stains |
Steel Wool | Hardwoods and softwoods | Tables, chairs, cabinets, frames | Light to medium burns |
Sanding | All wood types | Unfinished wood like tables, chairs | Medium to severe burns |
Planing | Hardwoods only | Intricate carvings, trim | Severe deep burns |
Wood Bleach | Hardwoods like oak, maple | Stained furniture like cabinets | Medium surface stains |
Restor-A-Finish | Finished woods | Tables, chairs, cabinets | Light to medium burns |
Wood Polish/Wax | All wood types | Finished furniture like tables, chairs | Very light surface burns |
Natural Remedies for Removing Burn Marks
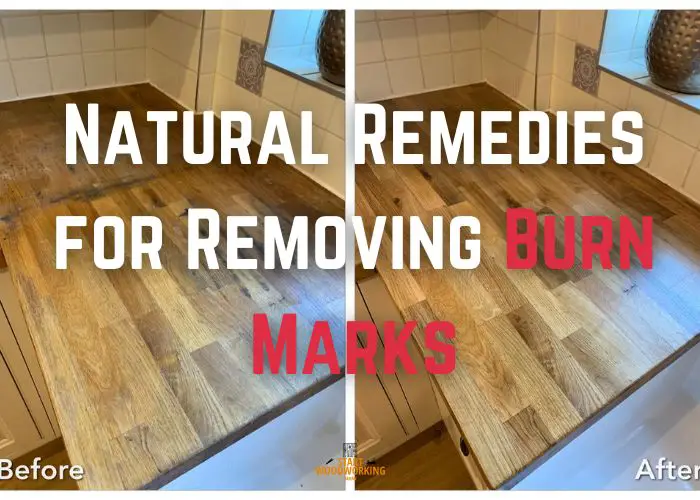
1. Mayonnaise
Materials:
- Real full-fat mayonnaise (avoid low-fat or light varieties)
- Small stainless steel bowl
- Clean, soft cotton rags (cut into 12×12 inch squares)
Step 1: Inspect the burn mark closely.
I inspect the burn area under bright halogen lights, running my fingers gently over the grain to feel the depth and texture.
Mayonnaise works best for light-to-medium marks on closed-grain woods like oak or maple. For severe furniture burns, I may need to sand or plane first.
Step 2: Gather Needed Materials
I collect a small stainless steel bowl and a jar of full-fat real mayonnaise, avoiding low-fat or light varieties that won’t work as well. I also gather several clean, soft cotton rags cut into 12×12 inch squares for smooth, even application and removal.
Step 3: Generously Apply the Mayonnaise
Using a spoon, I scoop a modest dollop of mayo onto the burned wood area. Then I slowly and gently rub the mayonnaise-coated rag directly over the burn mark. I like to work it into the grain with circular motions. The oil and acid in mayo can penetrate deeply to lift stains.
Step 4: Allow Enough Soaking Time
I set a timer for 45 minutes to ensure the mayo’s oils and acids have sufficient time to penetrate and loosen the burned material from deep within the wood fibers. Too short a time won’t allow for a full lift-off.
Step 5: Wipe Away Debris Thoroughly
Upon timer end, I use smooth, even strokes with a dry rag to sweep away all mayo and dark residue revealed after soaking. I inspect closely under light for any lingering stains.
Step 6: Reapply to Stubborn Areas
If needed, I focus a second or third coat of mayo on spots still showing burns, giving extra soaking attention to deep-seated stains.
Step 7: Buff and Inspect the Surface
Using a microfiber cloth, I give the treated area a final wipe and buffing to a satin sheen. Under lights, I minutely examine for any burns remaining.
Step 8: Consider Optional Conditioning
For dried wood, I sometimes follow with natural oil to replenish lost moisture from the burn and protect newly exposed.
Pros of Using Mayonnaise:
- Very gentle on the wood surface – Mayonnaise works without harsh abrasives, so it won’t further damage wood fibers or remove the original finish like sanding can. This makes it suitable for delicate antique pieces.
- Inexpensive and accessible ingredients – Mayonnaise is an affordable household staple found in every grocery store, as opposed to specialty chemical strippers.
- Multi-purpose formula – The blend of oils and acids in mayo makes it effective for both lifting burned material and conditioning the exposed wood afterward.
- User-friendly application – Mayo is easy to spread evenly by hand on any size burn without power tools or special equipment.
- Fast acting – Burns often lighten significantly after just one 45-minute application of mayo, where sanding can be more labor intensive.
Cons of Using Mayonnaise:
- Surface burns only – It only works for superficial burns that haven’t completely charred the wood. Deeper burns may require sanding first.
- Smelly process – The pungent smell of mayo can linger on wood and tools during soaking and cleanup.
- Not for high-gloss finishes – The oily residue left after mayo can dull polished finishes, so it’s best for natural wood.
- Time commitment – Waiting 45+ minutes for each application means the full process takes longer than one-step chemical strippers.
- Trial and error – Effectiveness varies with wood type and burn severity, requiring testing on sample pieces first.
2. Toothpaste and Baking Soda
Materials:
- Classic toothpaste (not gel or whitening varieties)
- Baking soda
- Small stainless steel bowl
- Clean, soft cotton rags (cut into 12×12 inch squares)
Step 1: Gather Needed Materials
I get a small stainless steel bowl, a jar each of baking soda and toothpaste (not gel or whitening varieties), and several soft cotton rags cut into 12×12 inch squares.
Step 2: Mix the Paste
In the bowl, I add one tablespoon each of baking soda and toothpaste. Using a spoon, I mix to a smooth, thick paste consistency, adding a bit more of each if too runny.
Step 3: Apply Paste to Burn Generously
I scoop a generous amount of paste onto the burn and slowly spread over the entire area with gentle, circular motions until fully and evenly coated 1/8 inch thick.
Step 4: Allow Paste to Soak for 30 Minutes
I set a timer and let the abrasive paste sit, allowing its ingredients time to work deep into the burn. Too short won’t fully lift charred material.
Step 5: Wipe Away Paste and Debris Thoroughly
Upon timer end, I use light pressure and smooth strokes with a dry rag to sweep away all paste, revealing any darkened residue lifted from the wood.
Step 6: Reapply Paste to Stubborn Areas
If needed, I focus extra coats of paste on spots still showing burns, giving deep-seated stains more soaking attention.
Step 7: Buff and Inspect the Surface
Using a microfiber cloth, I give the treated area a final wipe and buffing to a satin sheen. Under lights, I minutely examine for any burns remaining.
Pros of Using Toothpaste and Baking Soda:
- Inexpensive and accessible materials. Toothpaste and baking soda are affordable household items.
- Gentle abrasiveness. When combined, they create a non-toxic paste that removes burned material without damaging the wood surface.
- Easy application. The paste is simple to spread evenly by hand on any size burn area.
- Fast acting. Burns often lighten noticeably after a single 30-minute application.
- Conditioning properties. Toothpaste contains silica which helps buff and polish the wood while baking soda deodorizes.
Cons of Using Toothpaste and Baking Soda:
- Surface burns only. It only treats superficial burns, not deep charring that requires sanding.
- Messy process. The paste can be messy to mix, apply, and remove. Care must be taken to contain drips and residue.
- Temporary results. The burn may darken again over time as the surface finish wears away.
- Not for delicate woods. Toothpaste’s abrasives could potentially mar softer woods like pine.
- Varied effectiveness. Success depends on burn severity—may require multiple applications or switching methods.
- Dulling effect on finish. Residual paste can dull high-gloss urethane finishes if not thoroughly wiped away.
3. Cigarette Ash and Lemon Juice
Materials:
- Cigarette ash
- Fresh lemon juice
- Damp cloth
Step 1: Gather your supplies
Which include cigarette ash, lemon juice, and a damp cloth. A mixture of fresh lemon juice and cigarette ash makes an efficient burn treatment for wooden surfaces.
Step 2: Mix the cigarette ash and lemon juice together
In a small container, slowly mix one teaspoon of the finely ground cigarette ash with two tablespoons of lemon juice. Stir to form a thick paste consistency, similar to heavy cream or paint to paint so it can be easily applied to the burn mark. The mixture should be smooth and uniform.
Step 3: Use the damp cloth to soak up the ash-lemon juice paste.
Rub the cloth gently over the burn mark in circular motions. Apply light pressure so the paste is working into the burned area without damaging the surrounding wood grain. This mixture works to lift heat stains from the wood surface. According to my experience, this cuts through the carbon residue better than rubbing.
Step 4: Allow the paste to fully dry on the wood
This may take 15-30 minutes depending on how thickly it was applied. Once dry, inspect the burn mark. Repeat steps 2-3 if the burn is still visible. Multiple applications may be needed for severe burns.
Step 5: Clean the wood surface
Once the burn is fully removed, carefully buff the treated area with a microfiber cloth in the direction of the wood grain. This removes any residual ash particles. A final polish with lemon oil restores luster and protects the wood.
Step 6: Inspect your work
The burn should now be completely erased from the wood surface. For stubborn cases, light sanding may still be needed before finishing. But generally, this simple method does the trick.
Pros of Using Cigarette Ash and Lemon Juice:
- It is an inexpensive and natural method. Cigarette ash and lemon juice are inexpensive and commonly found household items.
- It works well for light burns. The acidity of the lemon juice helps lift heat stains from the wood’s surface. This makes it effective for minor burns.
- It polishes the wood. Not only does it remove burns, but the mixture polishes and restores the wood’s original luster.
Cons of Using Cigarette Ash and Lemon Juice:
- May require multiple applications. Severe or deep burns could need several rounds of treatment to fully remove. This makes the process more time-consuming.
- May darken the wood. Over-rubbing the mixture could unintentionally darken or stain the surrounding untreated wood area. Care needs to be taken.
- Not for all wood types. Hardwoods like oak may show lingering marks even after treatment. It works best on softer woods like pine that can be sanded.
Mechanical Techniques for Burn Mark Removal
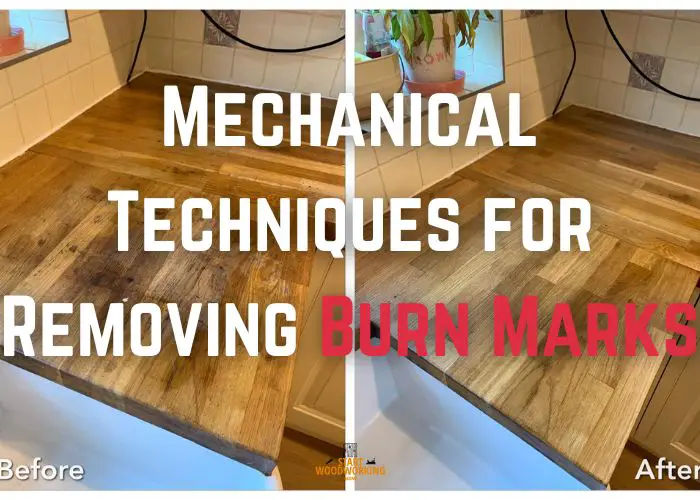
1. Steel Wool
Tools:
- Extra fine steel wool pads (either 0000 or 0000000 grade)
- Sanding block or foam pad
- Rag
- Vacuum suitable for wood dust
Materials:
- Mineral oil
- Clean rags
- Thick protective gloves
- Finishing oil (optional)
- Natural oil (optional)
Step 1: Examine the Burned Area Closely
I’ll inspect the burn under good lighting, running my fingers gently over the surface to feel the depth and texture. This allows me to determine if the burn is superficial scorching near the surface or a deeper char. A deep burn may require more sanding while steel wool could work for lighter scorches.
Step 2: Gather the Necessary Supplies
Collect extra fine steel wool pads, either 0000 or 0000000 grade for delicate work. Finer grades are less likely to damage the wood. I also gather mineral oil, which won’t leave a residue like other oils. Clean rags allow debris removal without scratching. Thick protective gloves shield my hands from any steel wool fibers that may break off.
Step 3: Clean the Surface
Using a dry, soft rag helps remove any dust or debris that could become embedded during steel wool rubbing. This prepares a clean base for the burn removal process.
Step 4: Dampen the Steel Wool
I squeeze a few drops of mineral oil onto the steel wool pad and rub it between my gloved fingers, working the oil thoroughly into all areas of the pad. This lubricates the abrasive fibers without making the pad dripping wet.
Step 5: Begin Rubbing Gently
I place the oiled steel wool pad directly over the burn mark and rub in slow, small circular motions, applying just enough pressure so the pad moves across the wood surface smoothly. Rushing could cause scratches.
Step 6: Remove Lifted Debris
As the burn darkens under abrasion, I regularly wipe away debris using an oiled rag, checking my progress until no more material lifts off. This keeps the surface clean.
Step 7: Inspect and Repeat if Needed
Under good lighting, I examine how much lighter the burn appears. If still noticeable, I reapply more focused steel wool rubs to the stubborn areas.
Step 8: Apply Finishing Oil
Once the burn is fully removed, I wipe a thin, even layer of oil over the entire treated area using a clean lint-free rag. This protects the exposed wood fibers.
Step 9: Consider Refinishing
For deep pre-existing stains or finishes, additional sanding and refinishing may be required after burn removal to achieve a uniform appearance. Light sanding and re-oiling alone often suffices for natural wood tones with light surface burns.
Pros of Using Steel Wool:
- It’s a gentle abrasion method that works well for light, surface burns without damaging the wood fibers.
- Steel wool rubs burn marks away smoothly without gouging or scratching like coarser abrasives could.
- It’s an economical option as steel wool is inexpensive and a small amount can treat many burned areas.
- The burn debris lifts off cleanly with an oiled rag, leaving a refined surface behind.
- With the right grade and technique, it preserves the wood’s natural texture and appearance.
Cons of Using Steel Wool:
- Steel wool is only effective on light, superficial burns. Deeper charring may require more sanding.
- The small abrasive particles can embed in the wood, so thorough cleaning is important.
- Over-rubbing risks creating fine scratches that need further sanding to remove.
- Trace rust particles from the steel can potentially stain some light-colored woods if not cleaned properly.
- For heavily stained or finished wood, additional sanding may still be needed to fully blend the surface after burn removal.
2. Sanding
Tools:
- Sanding block or foam pad
- Sandpaper ranging from coarse 60-grit to fine 220-grit
- Vacuum suitable for wood dust
Materials:
- Rag
- Mineral spirits
- Natural oil
Step 1: Examine the Burn Thoroughly
I closely inspect the burned area under bright lights, running my fingers along the grain to determine the depth and texture. This will help me choose the proper sandpaper grit.
Step 2: Gather Sanding Supplies
I purchase a sanding block or foam pad, several grits of sandpaper ranging from coarse 60-grit to fine 220-grit, and a vacuum suitable for wood dust. I also grab a rag and mineral spirits for cleaning.
Step 3: Start with Coarse Grit
Sanding Using 60-grit paper, I sand the burn area in straight, even strokes with moderate pressure. I sand just deep enough to remove the charred material but avoid gouging the wood.
Step 4: Progress to Finer
Grits Once the burn is gone, I step up sequentially through 100-, 150-, then 220-grit paper to smooth the sanded surface. With each new grit, I sand until buffed to a satin sheen.
Step 5: Vacuum and Inspect Frequently
Between each grit change, I vacuum away all dust then inspect under lighting. If any burns remain, I resand those spots only.
Step 6: Clean and Condition
To remove residual dust, I wipe with a mineral spirits-dampened rag. I then often follow up with natural oil to replenish lost moisture.
Step 7: Finish as Needed
For polished surfaces, I may further sand with 400-grit and apply fresh topcoat after the burn is fully erased.
Pros of Using Sanding:
- Most effective method – Sanding can completely eliminate all traces of burns, no matter the depth, unlike gentler options.
- Precise control – By sanding with a block or guide, it’s easy to target the burn area only without damaging surrounding wood.
- Customizable – Sandpaper grits can be selected to quickly remove material or finely buff as needed for the job.
- Thorough cleaning – It fully erases burns down to the bare wood, leaving a clean slate for refinishing.
Cons of Using Sanding:
- Labor intensive – Sanding requires physical effort and time, especially for large burn areas. It can be an arduous process.
- Risk of going too deep – It’s possible to oversand and permanently damage the wood if not careful along edges.
- Dust creation – Sanding produces significant fine wood dust that must be properly contained and cleaned.
- Not for delicate surfaces – More abrasive grits could potentially mar softer woods or carved details.
- Cannot preserve existing finish – The existing protective topcoat will be completely sanded through.
- Skill required – Proper sanding technique and sequencing of grits takes experience to get good results.
3. Planing
Tools:
Materials:
- Sandpaper (150-220 grit)
- Mineral spirits
- Natural oil
Step 1: Assess the burn mark.
Specifically note its depth, width and location on the wood surface. For a burn suitable for planing, it should be shallow, localized and on a flat surface. Deeper burns may require additional sanding after planing.
Step 2: Prepare the wood surface surrounding the burn mark.
Lightly sand in the direction of the grain with 150 grit sandpaper to smooth out any irregularities. This will allow for an even planing later.
Step 3: Prepare the Planer and Select a Blade
I installed a fresh, sharp planer blade suited for the wood type. Dull or wrong blades risk further damaging the surface.
Step 4: Adjust the depth setting of the plane
On my hand plane so that only a thin shaving is removed with each pass. The cut should be 0.01-0.02 inches deep maximum to avoid gouging the wood. Test the setting on scrap wood first.
Step 5: Test Cut on Unburned Wood
I run a small test piece through first to ensure the planer is set up correctly and the blade is performing well.
Step 6: Clamp the Burned
Board Securely Using my benchtop planer’s infeed table, I firmly clamp the board so it won’t kickback or vibrate during planing.
Step 7: Take Light Passes and Inspect
Starting with the burned side facing down, I make one very shallow pass. I inspect to check for full burn removal before taking additional light passes.
Holding the plane at a low angle, place it on the wood surface just outside one end of the burn mark. Maintaining steady pressure, pull the plane smoothly towards the other end in long, even strokes following the grain direction.
Step 8: Continuously Check Thickness
Using a caliper, I periodically measure the board to avoid overplaning and ensure an even thickness is maintained.
The burn will lighten with each shaving but may take several passes to fully clear it. Check that only the burn is being planed away and the surrounding wood is untouched.
Step 9: Finish to Desired Smoothness
Once the burn is gone, make a final few passes over the entire surface to even it out. Sand lightly with 150-220 grit paper to smooth the area and remove any remaining discoloration.
Step 10: Clean and Condition
I vacuum away shavings, wipe with mineral spirits if needed, then often treat with natural oil.
Pros of Using Planing:
- Very efficient method. With a single pass of a planer, deep burns can be removed quickly.
- Leaves a smooth surface. Properly planed wood will have an even, flat texture ready for finishing.
- Precise thickness control. A planer helps maintain consistent board thickness across burned and unburned areas.
- Cleans down to bare wood. Planing erases all burn residues thoroughly for a fresh surface.
Cons of Using Planing:
- Requires proper equipment. Access to a planer is necessary, which means more expensive than hand tools.
- Risk of tear-out. Burns near edges could splinter out if planer blades are dull or feeding pressure is too high.
- Not for delicate woods. Softer or carved woods may not survive repeated planing passes.
- Entire surface is impacted. Unlike localized sanding, planing reshapes the whole board, not just the burn.
- Dust is produced. Fine wood particles are ejected from the planer, requiring dust collection or cleanup.
- Safety concerns. Proper safety gear and technique is essential when using power planers.
- May leave grooves on burns. Aggressive planing can leave tracks that then require additional sanding.
Specific Products for Wood Burn Mark Removal
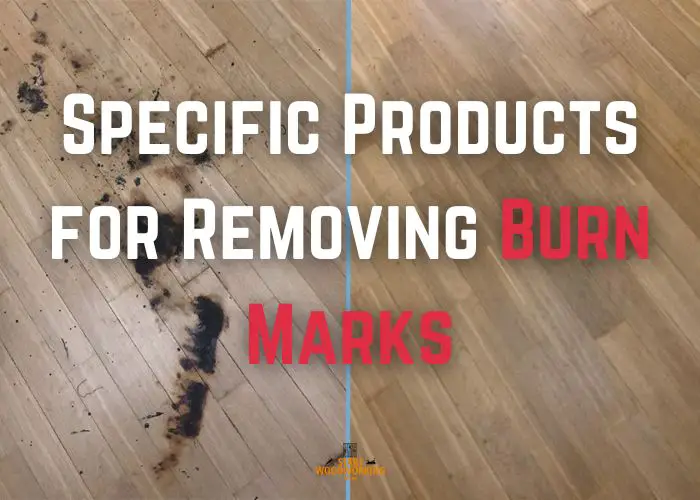
1. Wood Bleach
Tools:
- Small paintbrush or rag
Materials:
- Wood bleach
- Plastic sheeting
- Top-rated bleach like Howard’s Feed-N-Wax
- Clean rag
- Water for neutralizing
Step 1: Assess the burn for wood type and depth.
Wood bleach works best on closed-grain hardwoods for light-medium burns. For severe burns, I may need to sand or plane first to allow better bleach penetration.
Step 2: Gather Materials
Gather my supplies which include wood bleach, a small paintbrush or rag, and plastic sheeting. As an expert, I prefer a top-rated bleach like Howard’s Feed-N-Wax for its deep bleaching power.
Step 3: Apply the Bleach to the Burn Mark
Using slight upward strokes in the direction of the grain, I’ll carefully apply a thin coat of bleach directly over the burn mark using short brush or rag strokes. I take my time to fully saturate the affected area.
Step 4: Allow to Soak and Dry
Allow the bleach to fully dwell according to the product instructions, typically 1-4 hours. In this time, the active bleaching agents are working to lift the burned carbon residues to the wood surface.
Inspect the mark and reapply bleach if it hasn’t fully lightened. I sometimes wrap treated areas in plastic to allow the bleach to continue drawing out stains overnight for stubborn cases.
Step 6: Neutralize
Once satisfied, I’ll wipe the area with a clean rag dipped in water. This neutralizes the bleach while removing any residue or remaining discoloration.
Step 7: Inspect Results
If any faint shadow remains, I may repeat the process or progress to fine-grit sanding to refine the surface. With wood bleach, patience is key but results can be excellent.
Pros of Using Wood Bleach:
- Wood bleach is specifically formulated to lift stains from wood fibers, making it highly effective for lightening burns.
- It can remove burns from most common wood types including oak, maple, pine and more.
- With proper application, bleach will lift burns with minimal impact on the original wood color.
- It works well for both open and closed grain woods.
- Products like bleach pens allow precise application even in tight spaces.
Cons of Using Wood Bleach:
- Bleach must fully dwell to work, requiring several hours for deep burns versus faster methods.
- Results can vary significantly depending on wood type and burn severity. Deep burns may require multiple applications.
- Over-bleaching is possible, especially on softwoods. The wood surface needs to be monitored closely during treatment.
- Residual bleach fumes have strong odors and require proper ventilation during and after use.
- If not completely neutralized and removed, residual bleach can interfere with subsequent finishing.
- Not as effective on very darkly stained woods compared to lighter colors. May not fully erase deep burns.
2. Restor-A-Finish
Tools:
Materials:
- Restor-A-Finish
- Gloves
- Ventilation
- Mineral spirits
- Fresh topcoat (wax or polyurethane)
Step 1: Step 1: Inspect the Burn and Surrounding Finish
Inspect the burn closely and test Restor-A-Finish on a sample piece first. As an expert, I know it works well on most finishes and can sometimes lighten burns without full stripping.
Step 2: Test Product on Small Burn Area First
I apply a small amount of Restor-A-Finish to an inconspicuous spot and buff to test its effectiveness before treating the entire burn.
Step 3: Apply Thin Coat of Restor-A-Finish
Put on gloves and ventilate the area well. I’ll apply the product generously to the burn area with a lint-free cloth, working in small sections. Restor-A-Finish has strong fumes so safety is important.
Step 4: Allow to Haze Before Buffing
Allow it to dwell for 5-10 minutes to soften the existing finish and pull any stain particles to the surface. I check periodically and agitate with the cloth as needed.
Wipe off the dissolved finish and removed burn residues with a clean cloth. I wipe until no residue remains on the cloth and the burn is visibly lighter.
Step 5: Inspect and Reapply if Needed
For stubborn cases, I may reapply the product and extend the dwell time. Once satisfied, I buff the area to a satin sheen with 0000 steel wool.
Step 6: Clean Up
Inspect my work under natural light. Any remaining shadows can be removed through careful sanding and reapplication as needed. To remove residue, I wipe down the surface with a mineral spirits-dampened cloth and buff dry.
For protection, I always apply a fresh topcoat of wax or polyurethane following restoration with a product like Restor-A-Finish.
Pros of Using Restor-A-Finish:
- Works on most existing finishes without full stripping like polyurethane, lacquer, etc.
- Gentler method than bleaches – less risk of overworking the wood.
- Can lighten burns without affecting the surrounding finish or color.
- Easier to control application than bleaches due to brush/rag use.
- Dissolves and removes burn residues for a natural look.
- Conditioners help blend treated areas into the surrounding grain.
Cons of Using Restor-A-Finish:
- Requires adequate dwell time (5-10 mins) for deep burns versus faster methods.
- Results still depend on wood type and burn severity. May require multiple applications.
- Strong solvent fumes require ventilation and safety precautions.
- Not as effective on very dark stains as bleaches. May not fully erase deep burns.
- Residue needs complete removal before refinishing to avoid interfering.
- Not suitable if there are existing finish problems beyond the burn.
3. Wood Polish or Wax
Tools:
- Soft cloth
Materials:
- Paste wood wax or polish
- Mineral spirits
- Gloves
Step 1: Inspect the Burn Thoroughly
I closely examine the burn under bright light to determine its depth and texture. Polish/wax works best for superficial burns. I prefer a paste wax or furniture cream for this method.
Step 2: Gather Materials
I collect a high-quality paste wood wax or polish, a clean soft cloth, and mineral spirits for cleaning and softening wax. I wear gloves to keep my hands clean.
Step 3: Test the Product on a Small Area
I apply a small amount of polish/wax to a test spot using gentle buffing motions. This ensures it will effectively blend the burn without marring the wood.
Step 4: Apply a Thin Layer of Polish/Wax
Apply a thick layer of wax directly over the burn using gentle circular motions. Make sure to coat the entire burn area and slightly beyond.
Using long, even strokes, I spread a thin coat of polish or wax over the burn mark. I buff in the direction of the wood grain.
Using a soft cotton cloth, I begin buffing the wax in small sections. I apply firm pressure and focus my efforts over the burn mark, rubbing until the wax turns dark.
Step 5: Allow to Haze Before Buffing
Allow the wax to dwell for 5-10 minutes so it can penetrate into the wood fibers. During this time, I go over the whole piece to ensure even coverage.
Step 6: Inspect and Reapply if Needed
Under bright light, I examine for any remaining burn traces. For stubborn cases, I reapply wax and extend the dwell/buffing time. An electric buffer can speed things along. I buff until the burn is significantly lighter or fully removed against the surrounding grain.
Step 7: Clean and Condition Surface
Once satisfied, I give a final wipe-down with a tack cloth to remove any residue. I wipe off excess with a mineral spirits-dampened cloth and buff dry. The burn should now be seamlessly blended into the wood. This leaves the surface protected from within.
Pros of Using Polish/Wax:
- Wax and polishes are very gentle methods that don’t further damage or strip the wood.
- They work well for light surface burns on all wood types.
- Materials are inexpensive and easy to find at most hardware stores.
- With buffing, burns can be blended into the surrounding grain seamlessly.
- They condition and protect the wood surface at the same time.
Cons of Using Polish/Wax:
- Only effective for very light, surface-level burns. Deeper burns may require additional treatments first.
- The buffing process is labor-intensive, especially by hand. An electric buffer helps but isn’t always practical.
- Results depend on the woodworker’s skill – burns can be difficult to fully erase through buffing alone.
- Not as effective on darkly stained or painted woods compared to natural finishes.
- Burns may not fully vanish and may require follow up light sanding.
- Proper technique is needed to avoid accidentally burning the wood during vigorous buffing.
Type of Wood | How to Remove Burn Marks |
---|---|
Waxed wood | Use a piece of cork soaked in turpentine and rub the burned area with it. Once the wood burn is gone, put a coat of wax back on the wood. |
Lacquered wood | On modern lacquers, clean with a cloth dampened with soapy water, and if the burn stains resist add a few drops of household alcohol or bleach. On a more fragile lacquer pass a cloth impregnated with a mixture of 1/3 of gasoline and 2/3 of linseed oil. |
Varnished or Vitrified wood | Remove the burn marks by scraping the wood with a knife blade and then fill the hole with a wood paste in the color of the furniture. Rub gently with sandpaper to even the surface then apply a varnish of the same color. Or run a cloth impregnated with a mixture of 1/3 gasoline and 2/3 linseed oil on the stained varnished wood |
A great advantage is the possibility of only having to work on the affected area and not the entire parquet or piece of furniture.
See here exactly the steps how to Dissolve Wood Glue like a pro!
Tips for Preventing Burn Marks on Wood
- Always use sharp, clean blades and bits. Dull blades are more likely to tear or burn the wood surface.
- Go slowly, especially on harder or figured woods. Rushing causes friction that leads to burns.
- Apply wax or finish to the wood surface before machining. This reduces friction and protects the wood.
- Use proper dust collection when sanding. Fine dust is combustible and can ignite if it contacts hot blades or bits.
- Check for jammed wood chips regularly. Chips stuck in blades or bits cause excess friction and burning.
- Avoid feeding wood too quickly through machines like planers or jointers. Control the speed for smoother surfaces.
- Allow motors, blades and bits to fully stop before removing cut pieces. Kicking back wood can cause scorching.
- Wear appropriate safety gear like gloves, glasses and dust masks to prevent burns from hot surfaces or flying debris.
- Work in well-ventilated areas and keep wood dust under control to avoid accidental combustion.
- Inspect work areas for sources of sparks like loose wiring that could ignite dust buildup.
How to Remove Smaller Burn Marks from Wood?
Smaller burn marks can be removed from wood relatively easily from wood : First sand the stain off.
Second, run coarse and then finer sandpaper over the damaged wood area until the stain is completely removed.
Then polish the roughened surface and oil the wood if necessary.
How to remove a cigarette burn mark from wood?
To get rid of a cigarette burn on wood, you can start by putting baking soda on the burn.
Then lightly wet a clean cloth, wrap it around his index finger and rub the burn gently in a circular motion.
Repeat this operation quietly until the almost complete disappearance of the burn or the stain.
How to remove burn marks from wood with mayonnaise
Simply smear the damaged area with a dollop of mayonnaise, leave it on for about half an hour, rub it off well and then clean it with a soft cloth.
Repeat the process if necessary.
Finally, simply seal any unevenness with putty in the right color, flush with the surface.
How you can remove burn holes on the wooden floor?
- Sand using a piece of coarse sandpaper, something in the middle of the burn holes and along the edges off. However, do not deepen the holes. It is also not necessary to treat the entire wooden floor in the event of minor damage, just sand down until it is gone.
- Sand over the treated area with a fine piece of sandpaper so that the wood does not get too rough.
- Now remove the wood dust with a rag.
- Apply some stain to the burn holes in the wooden floor with a rag or sponge, to do this, choose the same shade as the entire floor.
- Now let the stain dry thoroughly.
- Roughen all the burn holes in the floor with the fine sandpaper again, but only very lightly, just enough to roughen the stain a little.
- Now apply the stain again.